Juneau Construction Company, a midsized, family-owned General Contractor located in the Southeast United States, specializes in higher education, commercial, and multi-use buildings. With over 63 excellence awards to their name, Wilson Haworth, Senior VDC Engineer, tells us that Juneau invests heavily in quality control processes to validate work, maintain deadlines, and disseminate information!
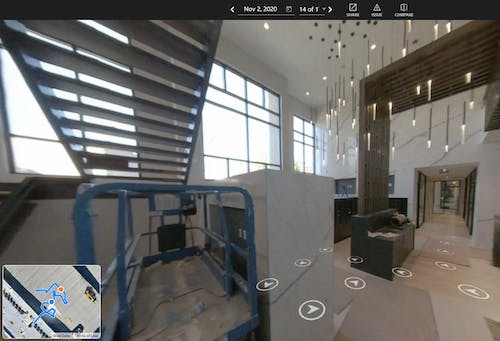
Knowing this, it’s unsurprising that the organization adopted drone technology in 2017 to utilize aerial and ground-based photography for conceptual modeling and coordination. What began as a drone hobbyist/Project Manager’s side project quickly turned into a fully operational drone program and, with DroneDeploy’s help, came to include 12 Part 107-certified pilots across six different states.
As their drone program grew, so did interest in more extensive reality capture. While its drone program was highly efficient, Juneau sought more comprehensive interior documentation to better communicate with project teams and stakeholders. “We lost data because there was no structure,” Wilson explained, “field personnel took pictures on smartphones and iPads and dumped them into Procore, leaving us with 30-100,000 pictures at the end of a project with no context.”
After a four-month trial process in which construction teams tested and scaled DroneDeploy’s 360 Walkthrough, the company rolled out this new method of data collection across each one of their job sites. Now, all owners, field personnel, and trade partners have the option to fully immerse themselves in the reality capture process and push critical items to Procore via the DroneDeploy integration. “It’s no longer one or two people’s responsibility on a project to circulate information,” Wilson said, “everyone is able to see that data.”
Read on as Wilson takes us through three of Juneau Construction’s most labor-intensive projects.
Visualizing Feedback in Real-Time
On one especially high-profile project, Juneau’s team had to navigate building a 1.5 million square foot, five-structure housing complex above a sprawling network of existing utilities. Directly next to the active college campus was a 60-year-old energy facility with a large steam tunnel located 20 feet below ground. With many workers and civilians alongside a potential safety hazard, the project team knew they had to provide real-time, valuable information to ease stakeholders’ concerns.
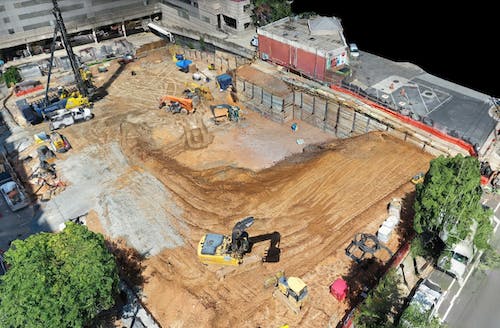
Combining current site documentation with drone flights, those involved with the project understood the limitations underground and could then track progress with ease. Because project team members were able to import building plans to Procore quickly and accurately, stakeholders received this information in minutes and could respond accordingly.
After receiving feedback that their interactive 360 panoramas expedited communication between field and office teams, Juneau took steps to make this process a new standard procedure for all of their projects.
The DroneDeploy solution keeps trade partners engaged.”
Wilson Haworth, Senior VDC Engineer, Juneau Construction
Tracking Assets Remotely
Additional challenges arose while building during the COVID-19 pandemic. With fewer field personnel available to monitor assets or equipment on-site, project teams had to get creative. On one 1.1 million square foot residential, retail, and parking complex, remote surveying was key to success. With a net-zero cut/fill goal, laborers had to keep track of a 1500 cubic yard stockpile, holding material that would be used later on in the project’s lifecycle.
By utilizing 360 Walkthrough, project teams and managers knew where that soil was on any given day via weekly drone reports and progress updates. “Once we get into the interior phase, we can now retroactively check our walkthroughs and identify any areas we may have missed,” Wilson stated. “Then we can directly send or tag this documentation to workers on-site through the Observation tab.” This kind of productivity could only be achieved through centralizing communication between the two platforms.
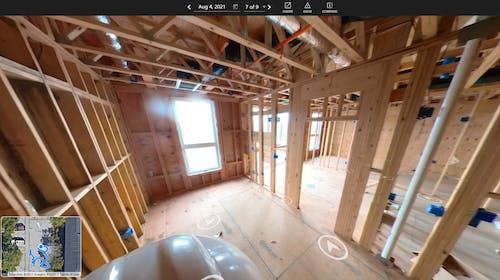
Managing Safety with Drone Flights
Building in a metropolitan area elicits significant constraints. For one 19-story structure, laborers had to dodge both civilian and environmental risks. Located 18 feet below the building, up against the storm vault and basement parking level, sat underground storage tanks for a nearby gas station. These tanks were just six inches away from the property line and posed considerable risks when installing the structure’s shoring walls. “Determining the correct elevation via DroneDeploy tools was crucial, because if we were off by a few inches, we could’ve had a huge environmental disaster on our hands,” Wilson explained. With limited space, using DroneDeploy in conjunction with 360 cameras throughout the course of construction was essential to project productivity and safety.
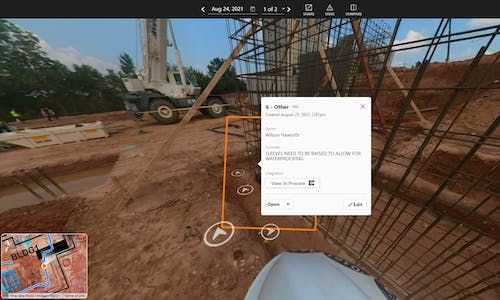
At the time of this article’s writing, Juneau Construction had just started work on their largest higher education project ever in South Carolina. DroneDeploy is a standard part of Juneau’s process from pre-bid to post-construction, and Wilson informs us that “field teams love to have data on-demand to know exactly what is on their site at any given time.” With all of their data in one place, project teams are proactive about getting weekly drone flights, daily walkthroughs, and progress pictures from the ground, and owners love seeing this shareable media. “DroneDeploy has helped us manage flights and stay within regulation,” Wilson said, “people know that if they want to see what a site looks like, they go to the DroneDeploy project.”
If you’re interested in learning more about drone use in construction, watch our webinar on how visual documentation streamlines your Procore Observations workflow, or contact us.