DroneDeploy
Blog
Learn from industry experts and customers in construction, energy, agriculture, and more. Get product updates and news from the DroneDeploy team.
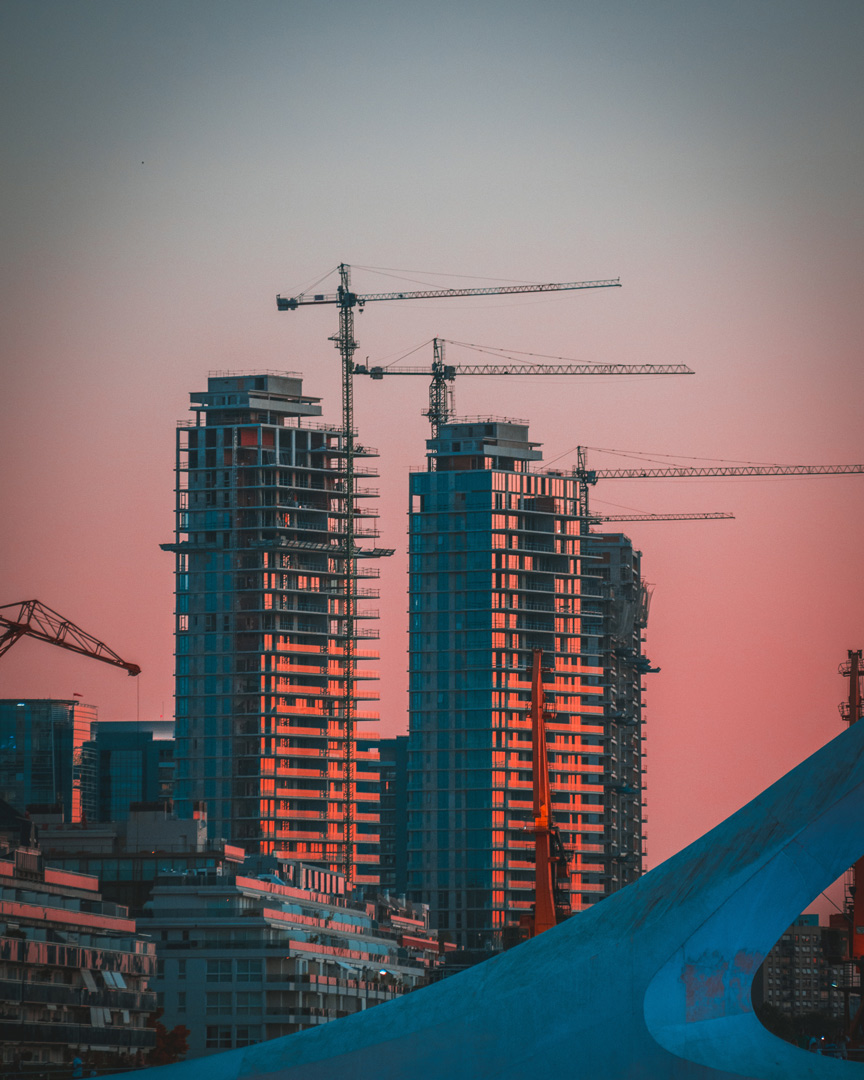
Thank you! Your submission has been received!
Oops! Something went wrong while submitting the form.